Stainless steel 316L VS 2205 duplex in biomedicine fields
The pharmaceutical and biotech industry has relatively high requirements about the steel materials used in processing vessel and pipeline system, that must have excellent corrosion resistance and cleanness to ensure the purity and quality of the drug product, they must also be able to tolerate the production environment and disinfection and cleaning processes of temperature, pressure and corrosion, also have good weldability and can satisfy the requirements of the industry of surface finish.
316L (UNS S31603, EN 1.4404) Austenitic stainless steel is the main material for equipment in the manufacturing of pharmaceutical and biotechnology industries. 316L stainless steel has excellent corrosion resistance, weldability, and electrolytic polishing properties, making it an ideal material for most pharmaceutical applications. Although 316L stainless steel performs well in many process environments, customers continue to improve the performance of 316L stainless steel through careful selection of specific 316L stainless steel chemical composition and the use of improved production processes such as electroslag remelting (ESR).
For highly corrosive media, customers who can accept increased maintenance costs can continue to use 316L stainless steel, or choose to use 6% molybdenum super austenitic stainless steel with higher alloy composition, such as AL-6XN® (UNS N08367) or 254 SMO® (UNS S31254, EN 1.4547). Currently, 2205 (UNS S32205, EN 1.4462) dual-phase stainless steel is also used in the manufacture of process equipment in this industry.
The microstructure of 316L stainless steel includes the Austenite phase and a very small amount of Ferrite phase, which is formed mainly by adding a sufficient amount of nickel to the alloy to stabilize the Austenite phase. The nickel content of 316L stainless steel is generally 10-11%. 2205 duplex stainless steel is formed by reducing the content of nickel to about 5% and adjusting the manganese and nitrogen added to form about 40-50% Ferrite and contains roughly the same amount of ferrite phase and austenite phase microstructure, with large to considerable corrosion resistance. The increase of nitrogen content and the fine grain microstructure of 2205 duplex stainless steel make it have higher strength than common austenitic stainless steels such as 304L and 316L. Under annealing conditions, the yield strength of 2205 duplex stainless steel is about twice that of 316L stainless steel. Due to this higher strength, the allowable stress of 2205 duple stainless steel can be much higher, depending on the design specifications for manufacturing process equipment. It can reduce wall thickness and cost in many applications. Let’s see the chemical composition and mechanical property comparison between 316L and 2205(specified in ASTM A240)
Grades | UNS | C | Mn | P | S | Si | Cr | Ni | Mo | N |
316L | S31603 | 0.03 | 2.0 | 0.045 | 0.03 | 0.75 | 16.0-18.0 | 10.0-14.0 | 2.0-3.0 | 0.1 |
2205 | S32205 | 0.03 | 2.0 | 0.03 | 0.02 | 1.0 | 22.0-23.0 | 4.5-6.5 | 3.0-3.5 | 0.14-0.2 |
Grades | Tensile strength, Mpa(ksi) | Yield strength Mpa(ksi) | Elongation | Hardness,HRB(HRC) |
316/316L | 515(75) | 205(30) | 40% | 217(95) |
2205 | 655(95) | 450(65) | 25% | 29331() |
Corrosivity performance
Pitting corrosion resistance
In pharmaceutical and biotechnology applications, the most common corrosion of stainless steel is pitting in chloride media. 2205 duplex stainless steel has higher chromium, molybdenum and nitrogen content, which is significantly better than 316L stainless steel in pitting and crevice corrosion resistance. The relative corrosion resistance of stainless steel can be determined by measuring the temperature (critical corrosion temperature) required for pitting in a standard test solution of 6% ferric chloride. The critical corrosion temperature (CPT) of 2205 duplex stainless steel is between 316L stainless steel and 6% molybdenum super Austenitic stainless steel. It should be noted that the CPT data measured in ferric chloride solution is a reliable ranking of the resistance to chloride ion pitting and should not be used to predict the critical corrosion temperature of the material in other chloride environments.
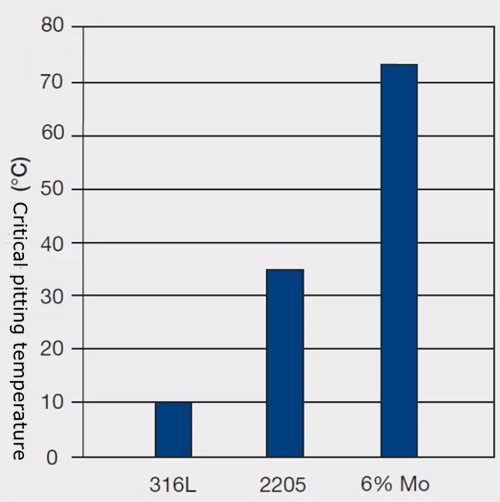
Stress corrosion cracking
When temperatures are higher than 150°F (60°C), 316L stainless steel is prone to crack under the combined action of tensile stress and chloride ions, and this catastrophic corrosion is known as chloride stress corrosion cracking (SCC). When selecting materials in hot fluid conditions, 316 stainless steel should be avoided in the presence of chloride ions and temperatures of 150°F (60°C) or above. As shown in the figure below, 2205 duplex stainless steel can withstand SCC at least 250°F (120°C) in a simple salt solution.
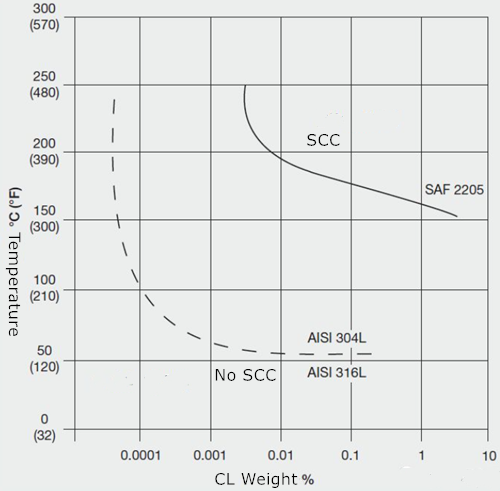
Processing properties
The machining of 2205 duplex stainless steel is similar to that of 316L in many ways, but there are still some differences. Cold forming processing must take into account the higher strength and work hardening characteristics of dual-phase stainless steel, equipment may be required to have a higher load capacity, and in operation, stainless steel 2205 will show higher resilience than standard austenitic stainless steel grades. The higher strength of 2205 duplex stainless steel makes it more difficult to cut than 316L.
2205 duplex stainless steel can be welded in the same way as 316L stainless steel. However, the heat input and interlaminar temperature must be strictly controlled to maintain the expected austenite-ferrite phase ratio and to avoid the precipitation of harmful intermetallic phases. The welding gas contains a small amount of nitrogen to avoid these problems. In the welding qualification of duplex stainless steel, the commonly used method is to evaluate the Austenite-ferrite ratio by ferrite tester or metallographic examination. The ASTM A 923 test method is typically used to verify the presence of harmful intermetallic phases. The recommended filler metal for the weld is ER2209 (UNSS39209, EN 1600). Self-fusion welding is recommended only if the weld solution annealing treatment can be performed after welding to restore corrosion resistance. It does not use filler metal. To perform solution annealing, the components are heated to a temperature of at least 1900°F (1040°C) and then rapidly cooled.
The penetration and fluidity of Duplex stainless steel 2205 are poor than 316L stainless steel, so the welding speed is slower and the shape of the joint needs to be modified. 2205 duplex stainless steel requires a wider groove Angle, a larger root clearance and a smaller blunt edge than 316L stainless steel in order to obtain a fully fused weld. If the welding equipment allows the use of filler wire, the 2209 filler wire is used to handle the track welding of 2205 stainless steel pipe, or the filler wire can be used instead of the appropriate alloying consumable insert.
Electrolytic polishing
Many pharmaceutical and biotech applications require the surface in contact with the product to be electrolytically polished, so high-quality electrolytically polished surfaces are an important material property. 2205 Duplex stainless steel can be electrolytically polished to a finish of 15 microinches (0.38 microns) or higher, which exceeds the ASME BPE standard for surface finish of electrolytically polished surfaces, but the electrolytically polished 2205 stainless steel surface is not as bright as 316L stainless steel surface. This difference is due to the slightly higher metal solubility of ferrite compared to austenite during the electropolishing process.