How to weld TP310HCbN(HR3C) steel?
Stainless steel grade TP310HCbN also referred as HR3Csteel, has much higher strength than conventional 310 stainless steels utilizing finely dispersed M23C6 and NbCrN, the 25Cr-20Ni chemical composition offer much better steam oxidation resistance than 18Cr-8Ni Austenitic stainless steels. TP310HCbN Austenitic heat resistant steel is widely used in superheater and reheater systems with an operating temperatures higher than 620℃ in ultra-supercritical thermal power boiler units. These harsh conditions require that the steel and its weld have sufficient high temperature endurance strength, creep strength, corrosion resistance and steam oxidation resistance. In some cases, thermal crack sensitivity of welding, stress corrosion crack sensitivity of joint and aging embrittlement tendency of joint often occur in the process of construction. A lot of practice shows that nickel-based Austenite welding materials have been widely used in engineering to weld TP310HCbN.
Weldability of 310HCbN(HR3C) steel
In terms of chemical composition (see table below), HR3C steel is formed by limiting the content of C and adding 0.20% ~ 0.60% of strong carbonitriding to form Nb and 0.15% ~ 0.35% of N. 25Cr-20Ni steel is strengthened by precipitation of Nb intermetallic compound NbCrN and Nb carbon, nitrogen compound and M23C6 carbides. The mechanical properties of the steel at room temperature,the tensile strength and yield strength are 750 MPa and 373 MPa respectively, and the elongation after fracture is 45%.
According to the test results, when using erNICR-3 wire, the welding joint is often broken in the weld metal; The welded joints of Ernicrcomo-1 and ErnicRMO-3 often break at the base metal. Therefore, ERNICRMO-3 and ERNICRcomo-1 welding materials are recommended.
Grades | C | Cr | Ni | Nb | N | Si | Mn | P | S |
HR3C base steel | ≤0.1 | 12.0-27.0 | 17.0-23.0 | 0.2-0.6 | 0.15-0.35 | ≤1.5 | ≤2.00 | ≤0.03 | ≤0.03 |
ERNiCr-3 | 0.016 | 20.65 | 73.2 | 2.6 | / | 0.09 | 3.2 | 0.001 | 0.001 |
ERNiCrMo-3 | 0.01 | 21.8 | 64.8 | / | / | 0.06 | 0.02 | 0.006 | 0.006 |
ERNiCrCoMo-1 | 0.08 | 22 | 55 | / | / | 0.1 | 0.1 | 0.002 | 0.002 |
In the high-temperature performance, as a result of long-term aging process between the tiny metal NbCrN very slow growth rate and M23C6 phase dispersion precipitates (have good organizational stability), which have a good strengthening effect, and appear harmful sigma and Cr2N phase probability is small, so the HR3C steel has high high-temperature creep rupture strength and high allowable stress. At the same time, Cr element is easy to combine with oxygen on the surface of the material to form a Cr2O3 oxide surface, which prevents the continuous oxidation of steel, so the steel has better high-temperature steam corrosion resistance and flue gas corrosion resistance. It is suitable for the end pipes of superheater and reheater parts of ultra-supercritical boilers with steam parameters of 621℃ and 31MPa. The supply state of the steel is solution treatment (1200℃ for 30min), the microstructure is Austenite matrix + fine dispersion distribution of precipitated phase (M23C6, NbCrN, etc.). However, this does not mean that satisfactory joint performance will be achieved in all cases. The research shows that the main problems of the weldability of the steel are:
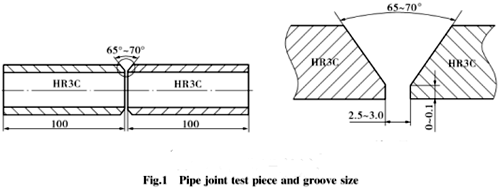
1. Sensitivity to hot crack.
The microstructure of pure Austenite has a great tendency to form welding hot cracks, that includes crystallization cracks in the weld metal, high temperature liquefaction cracks in the heat-affected zone of welding heat affected zone (HZZ) or in the heat-affected zone of the front pass in the back pass of multi-layer welding, and high temperature brittle cracks formed in the HZZ under stress due to insufficient plasticity. This depends on the impurity content of the base metal and the filler metal composition, especially sulfur and phosphorus. Although the tendency of welding hot crack is not large because of the low content of sulfur and phosphorus impurities in the weld and base metal, the crystallization crack is especially easy to occur in the arc part and the arc pit of the weld.
2. Stress corrosion crack sensitivity of joints.
Damage accidents caused by stress corrosion are often heard for the coal-fired power stations. The temperature range of Cr-Ni austenitic steel most prone to stress corrosion is 50 ~ 300℃, after the welding of the joint to the boiler heating operation during the period of time, the welded joint is prone to stress corrosion cracks. The results show that the stress corrosion behavior of HR3C steel welded joints increases significantly in NaCl solution, indicating that Cl- has a great influence on the stress corrosion sensitivity of the joints.
3. Aging embrittlement tendency of joints.
Boiler superheater and reheater components made of HR3C steel may operate at temperatures up to 650℃ or above, just within the precipitation temperature zone of the austenitic intermetallic phases such as σ phases. A small amount of σ phase in the joint will cause a sharp decrease in creep fracture strength and plasticity and accelerate the early failure of key components.
In summary, the main problems of 310HCbN steel weldability are the heat crack sensitivity of welded joints and stress corrosion crack sensitivity of welded joints. At the same time, the aging embrittlement tendency of the joint should not be ignored. Selecting high-quality and suitable welding materials and optimizing the welding process are important technical means to control and improve the weldability of the steel. Its weldability is equivalent to TP347H, and matching welding consumables is available.
Engineering case of 310HCbN steel welding
Example 1
There are 198 310HCbN steel welding joints on the first-stage superheater and second-stage superheater of a 1000MW ultra-supercritical thermal power unit boiler, among which 66 are the first-stage superheater with the specification of φ48mm×9.5mm and 132 are second-stage superheater with the specification of φ 60mm × 4.2mm. The pipe joint is a 65°V groove butt joint, as shown in the figure. Using φ 2.4mm ERCrNI-3 nickel-based wire, strict interlayer temperature and welding process parameters. The welding joint passed the appearance inspection and ray inspection successfully, and the welding quality was 100% qualified.
Example 2
SA213-TP310HCbN steel is welded with nickel base wire ErNiCrCoMo-1. In the installation project of furnace no.3 of a 2×660 MW ultra-supercritical unit, the final superheater and final reheater outlet transition section were made of HR3C steel, and the specifications were 47.6mm × 9mm, 41.3mm× 8mm, 52.2mm × 5mm, 63.5mm × 7.3mm. The pipe joint is a butt joint with a 60° to 70° V-shaped groove (a total of 1546 welding joints, horizontal welding positions). It not only ensures the protection effect of filling argon at the root of the weld, prevents the oxidation phenomenon at the root, but also eliminates the concave defect of the root joint welded joints, and ensures its good formation. The joint was tested by 100%RT, and the first pass rate reached 98.6%.
Example 3
Thermanit 617 and YTHR3C wire welded joints were tested for high temperature and short time strength of HR3C steel. YT-HR3C welding material is produced by Nippon Steel Sumitomo Welding Industry Co., LTD., which is expensive and needs to be imported. Two kinds of welding wire (YTHR3C and Thermanit 617) welding joint specimens were subjected to short-term strength test at high temperature (550℃, 600℃, 625℃, 650℃). The results show that the short-time strength of the joint welded with nickel base alloy Thermanit 617 is higher than that of YT-HR3C, and the tensile fracture of the former specimen is located in the base metal region, while the latter is in the weld.