Советы по сварке аустенитной нержавеющей стали
Аустенитная нержавеющая сталь является наиболее широко используемым типом нержавеющей стали, в основном Cr18-Ni8, Cr25-Ni20, Cr25-Ni35. Сварка аустенитной нержавеющей стали имеет очевидные характеристики:
- Сварка горячих трещин.
Аустенитная нержавеющая сталь легко образует громоздкую столбчатую зернистую структуру, когда сварочные соединения частей высокой температуры и время удержания больше из-за малой теплопроводности и большого коэффициента линейного расширения. В процессе затвердевания, если содержание серы, фосфора, олова, сурьмы, ниобия и других примесных элементов выше, это приводит к образованию эвтектики с низкой температурой плавления между зернами. Когда сварное соединение подвергается высокому растягивающему напряжению, в сварном шве легко образуются трещины затвердевания, а в зоне термического влияния - трещины сжижения, которые являются сварочными термическими трещинами. Наиболее эффективным методом предотвращения горячих трещин является уменьшение примесных элементов, которые легко образуют эвтектику с низкой температурой плавления в стали и сварочных материалах, и чтобы аустенитная нержавеющая сталь Cr - Ni содержала ферритную структуру 4% ~ 12%.
- Межкристаллитная коррозия.
Согласно теории истощения хрома, осаждение карбида хрома на межкристаллитной поверхности, приводящее к истощению хрома на границе зерен, является основной причиной межкристаллитной коррозии. Поэтому выбор марок с ультранизким содержанием углерода или сварочных материалов, содержащих стабилизированные элементы, такие как ниобий и титан, являются основными мерами по предотвращению межкристаллитной коррозии.
- Коррозионное растрескивание под напряжением.
Коррозионное растрескивание под напряжением (КРН) обычно представляется как хрупкое разрушение, причем время обработки разрушения короткое, а повреждения серьезные. Сварочное остаточное напряжение является основной причиной коррозионного растрескивания под напряжением в аустенитной нержавеющей стали. Причинами также являются изменение микроструктуры сварного соединения или концентрация напряжения в местной коррозионной среде.
- σ фазовое охрупчивание сварных соединений
σ-фаза - это вид хрупкого интерметаллического соединения, которое в основном сосредоточено на границе зерен столбчатых зерен. Для Cr-Ni аустенитной нержавеющей стали, особенно для Ni-Cr-Mo нержавеющей стали, она склонна к δ-σ фазовому переходу, и изменение будет более очевидным, когда содержание δ феррита в сварных швах более 12%, делая очевидным охрупчивание в металле шва, поэтому количество дельта феррита в наплавочном слое стенки горячего реактора гидрогенизации будет контролироваться в 3%~10%.
Какой сварочный материал подходит для сварки нержавеющей стали марки 304?
Сварочный материал типа 308 рекомендуется использовать при сварке нержавеющей стали 304, поскольку дополнительные элементы в нержавеющей стали 308 могут лучше стабилизировать зону сварки. провода 308L также являются приемлемым вариантом.
Содержание углерода в низкоуглеродистой нержавеющей стали составляет менее 0,03%, в то время как стандартная нержавеющая сталь может содержать до 0,08% углерода. Производители должны уделять особое внимание использованию сварочных материалов с L-углеродом, поскольку низкое содержание углерода в них снижает склонность к межкристаллитной коррозии. Производители для сварки GMAW также используют сварные швы 3XXSi, такие как 308LSi или 316LSi поскольку Si улучшает смачивание сварных швов. В случаях, когда сварное соединение имеет высокий горб или плохое соединение в ванне у носка галтели или нахлесточного шва, использование проволоки с воздушной защитой, содержащей Si, может увлажнить сварной шов и увеличить скорость осаждения. Сварочные материалы типа 347 с небольшим содержанием Nb могут быть выбраны, если рассматривается возможность выпадения карбидных осадков.
Как сваривать нержавеющую и углеродистую сталь?
Некоторые конструктивные детали привариваются к поверхности углеродистой стали с антикоррозийным слоем для снижения затрат. При сварке углеродистой стали с легированным основным металлом использование сварочного материала с более высоким содержанием сплава может сбалансировать степень разбавления в сварном шве. Например, при сварке углеродистой стали и нержавеющей стали 304 или 316, а также других разнородных нержавеющих сталей, подходящим выбором является проволока или электрод 309L.
Если вы хотите получить более высокое содержание Cr, используйте 312 сварка материал. Следует отметить, что скорость теплового расширения аустенитной нержавеющей стали 50% выше, чем у углеродистой стали. При сварке разница в скорости теплового расширения будет создавать внутреннее напряжение, что приведет к образованию трещины. В этом случае необходимо выбрать подходящий сварочный материал или определить соответствующий процесс сварки (рис. 1). Это показывает, что при сварке углеродистой и нержавеющей стали деформация коробления, вызванная разной скоростью теплового расширения, требует большей компенсации.
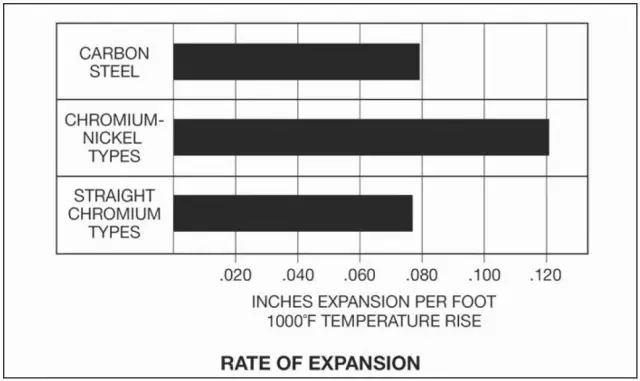
Какова надлежащая предварительная подготовка к сварке?
Перед сваркой используйте бесхлорный растворитель для удаления смазки, следов и пыли, чтобы избежать коррозионной стойкости основного материала нержавеющей стали от углеродистой стали. Некоторые компании используют раздельное хранение нержавеющей и углеродистой стали, чтобы избежать перекрестного загрязнения. Если для очистки области вокруг скосов используются специальные шлифовальные круги и щетки из нержавеющей стали, иногда необходимо выполнить вторичную очистку швов. Поскольку операция компенсации электродов при сварке нержавеющей стали сложнее, чем при сварке углеродистой стали, очистка шва имеет большое значение.
Какова правильная обработка после сварки?
Прежде всего, напомним, что причина, по которой нержавеющая сталь не ржавеет, заключается в том, что Cr и O реагируют на поверхности материала, образуя слой плотного оксидного слоя, и играют защитную роль. Ржавчина нержавеющей стали возникает из-за осаждения карбида и нагрева в процессе сварки, что приводит к образованию оксида железа на поверхности сварки. Совершенные сварные соединения в состоянии сварки могут также образовывать подрезы в ржавой области на границе зоны термического влияния сварки в течение 24 часов. Поэтому для регенерации нового оксида хрома нержавеющую сталь после сварки необходимо полировать, травить, шлифовать или промывать.
Как контролировать выпадение карбидных осадков в аустенитной нержавеющей стали?
Когда содержание углерода превышает 0,02% при 800-1600℉, C диффундирует к аустенитным границам зерен и реагирует с Cr на границах зерен с образованием карбидов хрома. Если большое количество Cr отверждается элементом C, коррозионная стойкость нержавеющей стали снижается, и при воздействии коррозионной среды возникает межкристаллитная коррозия. Результаты эксперимента показывают, что межкристаллитная коррозия возникает в зоне термического влияния сварки в резервуаре для воды с коррозионной средой. Использование сварочных материалов с низким содержанием углерода или специальных сплавов может снизить склонность к выпадению карбидов и повысить коррозионную стойкость. Nb и Ti также могут быть добавлены для затвердевания C. По сравнению с Cr, элементы Nb и Ti имеют большее сродство с C. класс347 сварочный материал предназначен для этой цели.
Почему провода из нержавеющей стали магнитятся?
Нержавеющие стали с полностью аустенитной структурой немагнитны. Однако при более высокой температуре сварки зерна в микроструктуре становятся крупнее, и восприимчивость к трещинам после сварки увеличивается. Чтобы снизить чувствительность к термическим трещинам, производитель сварочных материалов добавляет в сварочный материал ферритообразующие элементы (рис. 2). Ферритная фаза уменьшает размер зерна аустенита и повышает трещиностойкость. На следующем рисунке показана ферритная фаза (серая часть), распределенная на аустенитной матрице в сварочном материале 309L.
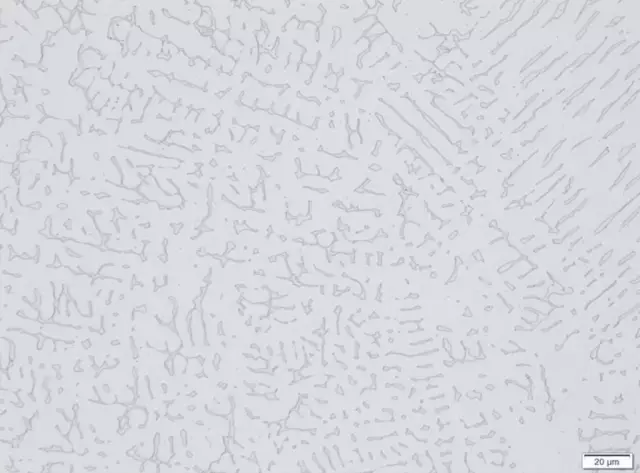
Магнит не прилипает прочно к металлу аустенитного шва, но при броске чувствуется небольшое присасывание. Это также наводит некоторых пользователей на мысль, что продукт неправильно маркирован или что используется не тот материал припоя (особенно если этикетка снята с упаковки). Количество феррита в сварочном материале зависит от температуры эксплуатации. Избыток феррита, например, снижает вязкость при низких температурах. В результате количество феррита для сварочных материалов марки 308, используемых в трубопроводах СПГ, составляет от 3 до 6, в то время как количество феррита для стандартных сварочных материалов типа 308 составляет 8. Одним словом, сварочные материалы могут выглядеть одинаково, но даже небольшие различия в составе иногда могут иметь большое значение.